- +2348034026015
- info@nigerianfoundriesgroup.com
- Mon - Fri: 8:00 - 17:00
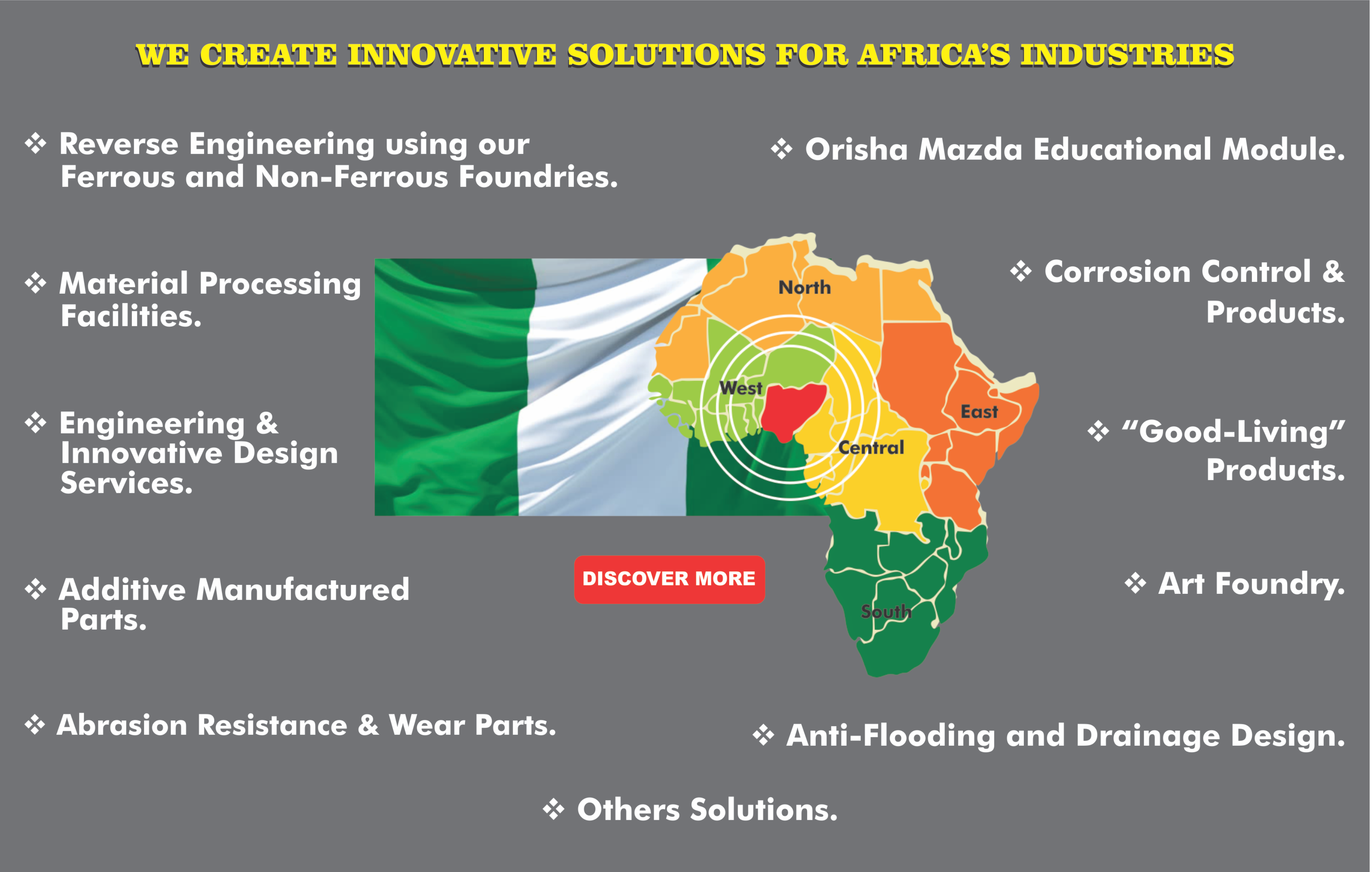
HISTORY TIME LINE OF THE ENGINEERING PIONEERS OF AFRICA
1960s
The Africa Calling of the two Barberopoulos brothers
Romeo leaves Greece in 1956 to work for the Leventis Group in Nigeria, while John works briefly in Ghana and emigrates to Canada in 1964. Romeo buys land in Ilupeju and starts in 1967 Industrial Application Ltd, the first Plastic Sandal Manufacturing Company of its kind in Nigeria.
In 1967 in Canada during Expo '67, the two brothers decided to incorporate Nigerian Foundries Ltd (NFL) in 1969. The two brothers had a vision for the fast-growing and promising nation of Nigeria.
Nigerian Foundries becomes a reality.
.
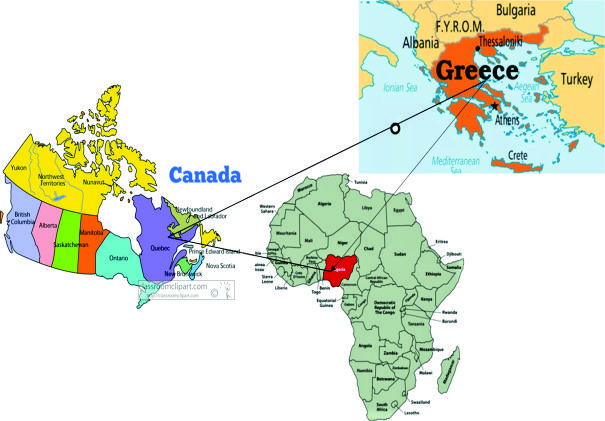
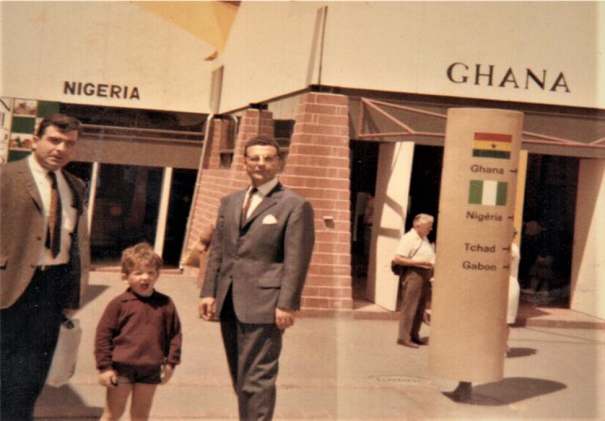
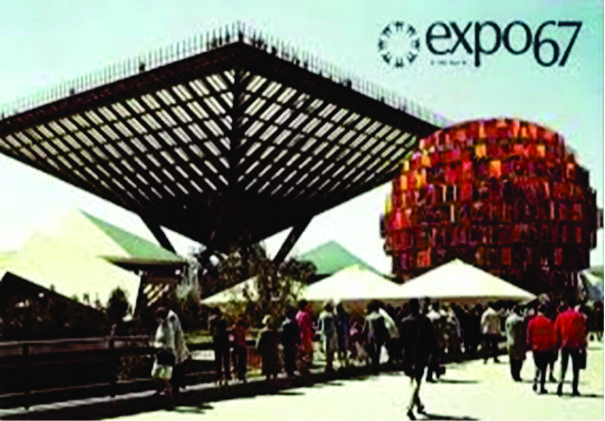
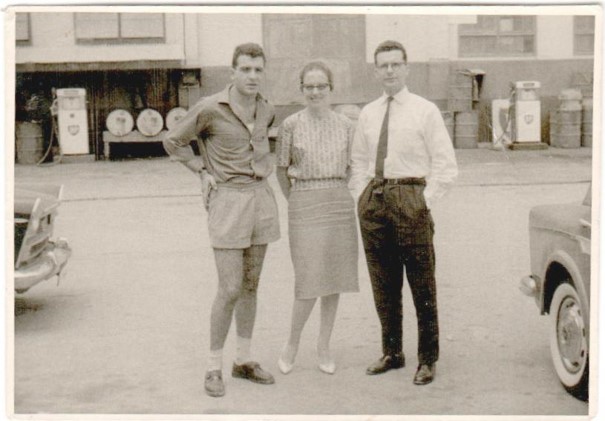
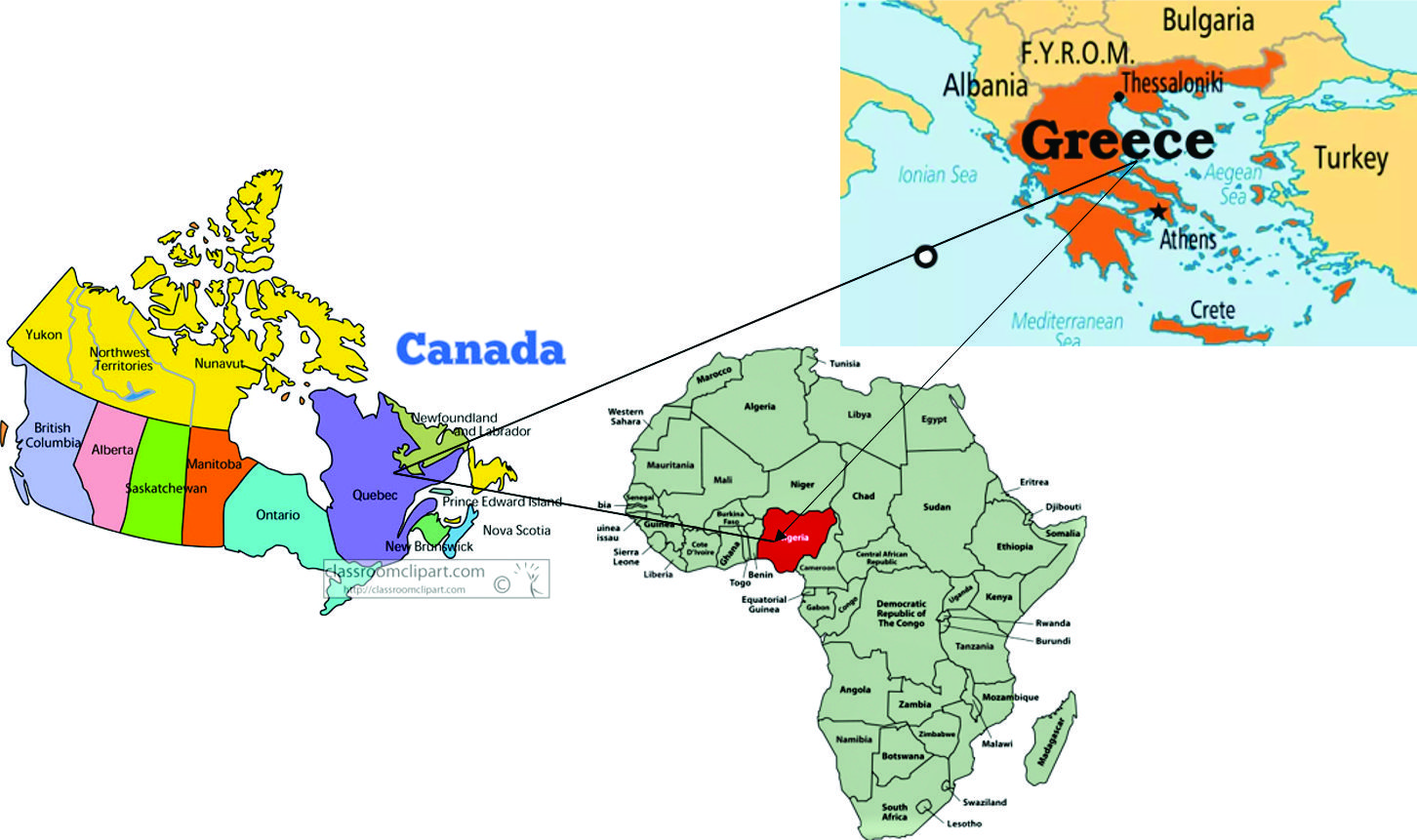
1970–1979s
Nigerian Foundries becomes a reality.
Both brothers build their first cupola (coke) oven at Ilupeju. The foundry was basic using hand molding and patterns crudely made with skills from carpentry school. Some experienced personnel came from the Nigerian Railways Foundry set up during the Colonial times.
In I974, the first significant expansion was to purchase two one-ton rotary furnaces, two Zimmerman Molding lines with tracts, overhead ladle movement & a primary machine shop. The oil boom of the 1970s in Nigeria opens substantial business opportunities for both local and foreign entrepreneurs. Five vehicle assembly plants are set up amongst other industries. The two brothers dream big and, in 1977, acquire 56 acres of land next to the NNPC refinery in Kaduna. Discussions are concluded with GKN of the United Kingdom to set up a Joint Venture automotive foundry to supply Peugeot, Fiat, and Volkswagen with casted parts.
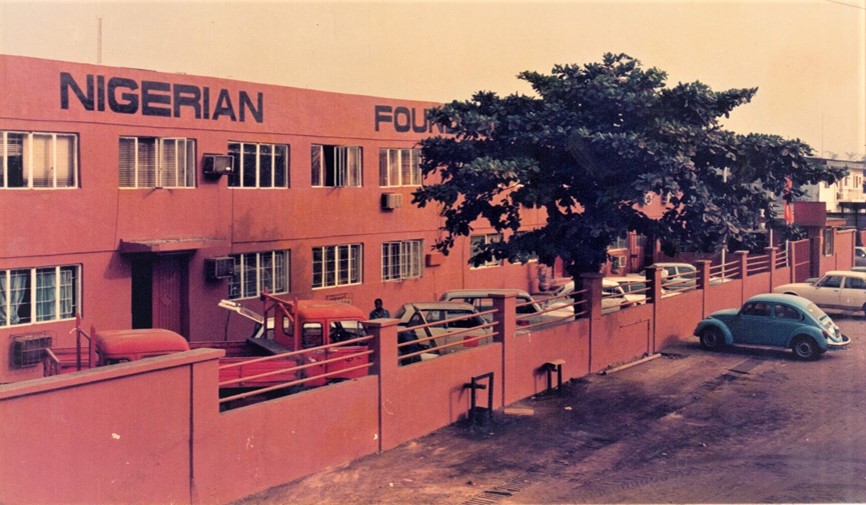
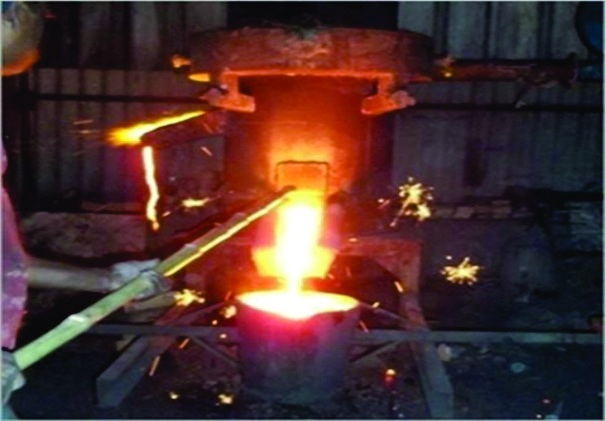
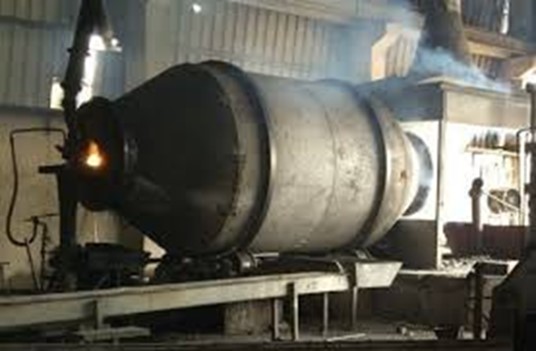
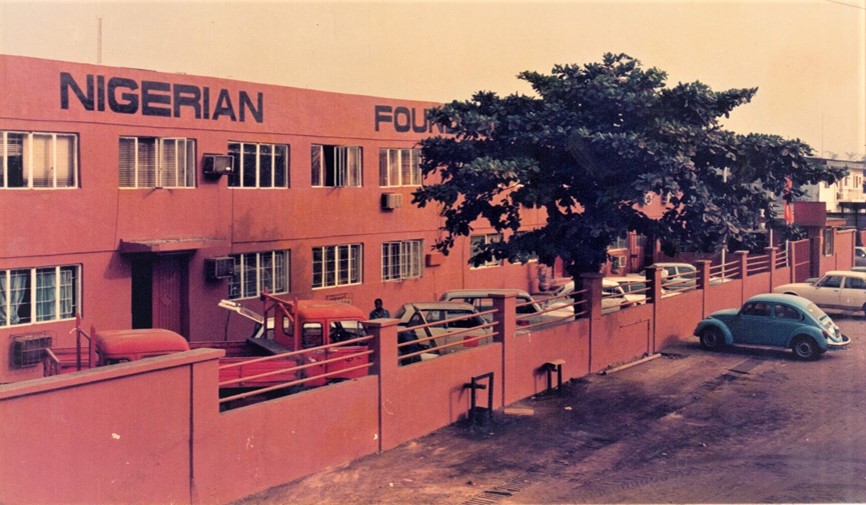
1980s
The World Oil boom economy plunges into worldwide recession!
The Nigerian Economy by the early 1980s takes a serious plunge with massive perpetual devaluations. Plans for the Kaduna expansion get abandoned. GKN (automotive division) files for receivership in the UK. NFL enters into survival mode and begins diversifying. By the mid-1980s, NFL, through a DIFFRI, UNICEF, & World Bank initiative, develops the Nigerpump Mark 2 handpump for mass use in Rural areas. It gears up and produces 6000 pumps per annum. In 1988 NFL, with funding from the Nigerian Industrial Development Bank (Present BOI), expands to making Steel and iron Alloy castings for the Cement Industry. This encouragement came from West African Portland Cement (WAPCO) under the UK's Blue Circle Group, which is today LafargeHolcim. A bold move during times of a Nigerian and World recession.n.
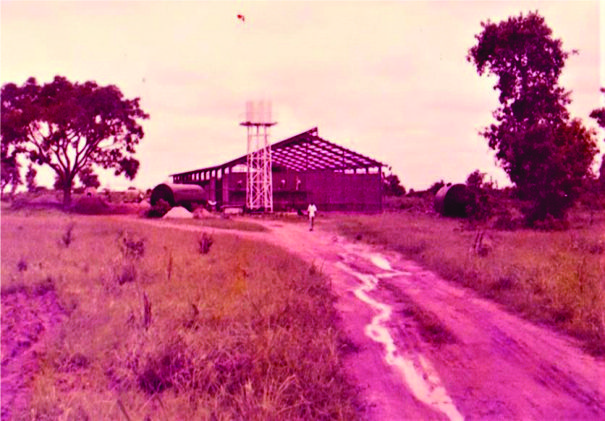
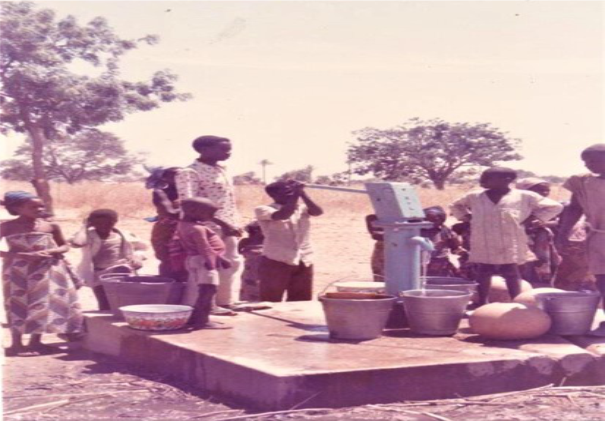
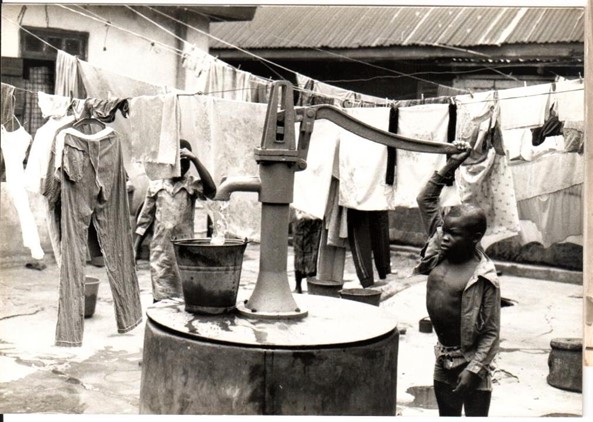
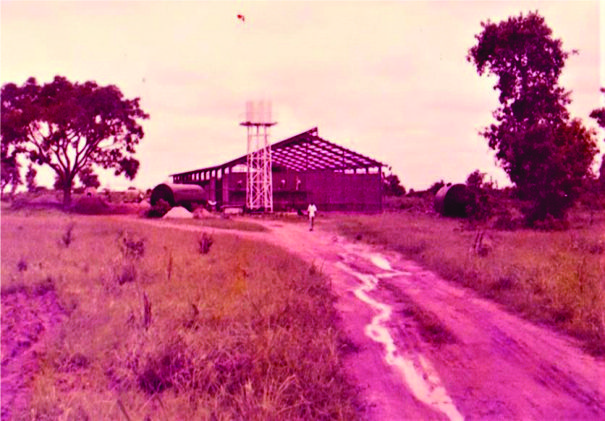
1990s
New Foundry expansion, new technologies, it's the time to innovate.
In 1991 the NIDB foundry expansion became operational. The technical consultant was Mr. Southwick, who had retired from Bradley and Fosters of the United Kingdom. Mr. Southwick was one of the Pioneers of High Chrome Irons' development with Magotteaux of Belgium in the 1960s. The expansion includes Induction Furnaces, Metallurgical Laboratories, mobile equipment, and machine-shop facilities.
In 1995 NIDB supported NFL with another loan to expand its melting capacity by purchasing additional furnaces, cranes, and ancillary equipment. West African Portland Cement, since 1985, due to the lack of foreign exchange availability, has been instrumental in NFL's development as a Local Content Manufacturers. In 1995 Romeo registered the Foundry Association of Nigeria, in which 45 foundries are registered, and two international conferences were held.
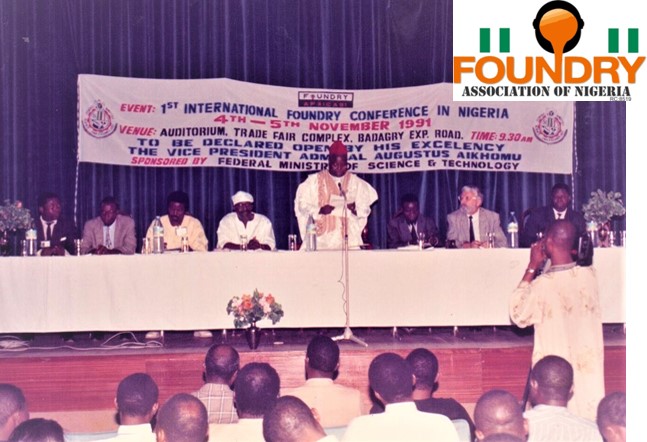
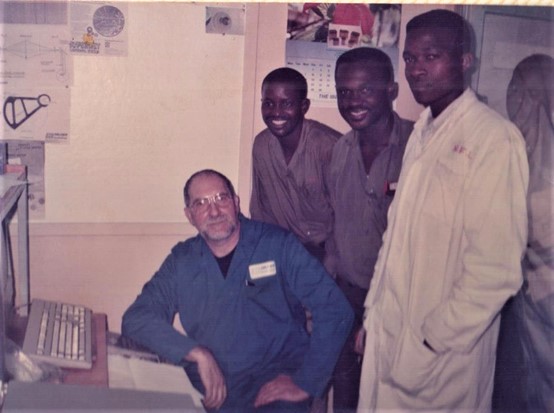
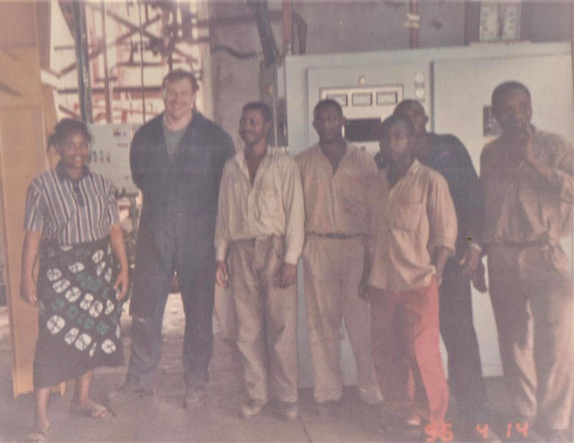
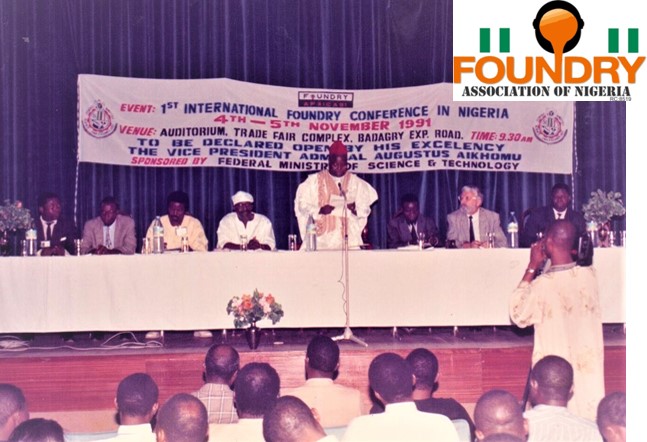
1996-1999
A movement to Manganese steel and expansion of horizons
West African Portland Cement is happy with the technological progress of the NFL. It decides to purchase 12.5% of NFL shareholding so that it can secure its future castings supply. NFL with German Consultants moves into manganese steel and making castings for Mines and Quarries. In 1998 NFL purchases Adebowale foundries in Otta, which Germans had built in the mid-1970s. During that time, NFL exports castings to Ghana and Niger and acquires the MAVIS Casting Simulation Program, a state-of-the-art software developed for the International Foundry Industry. .
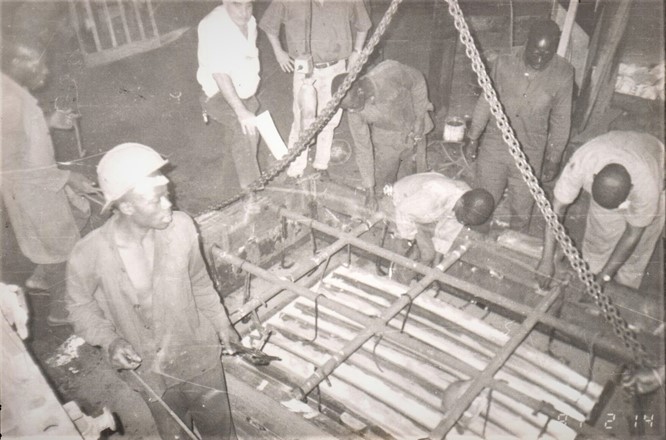
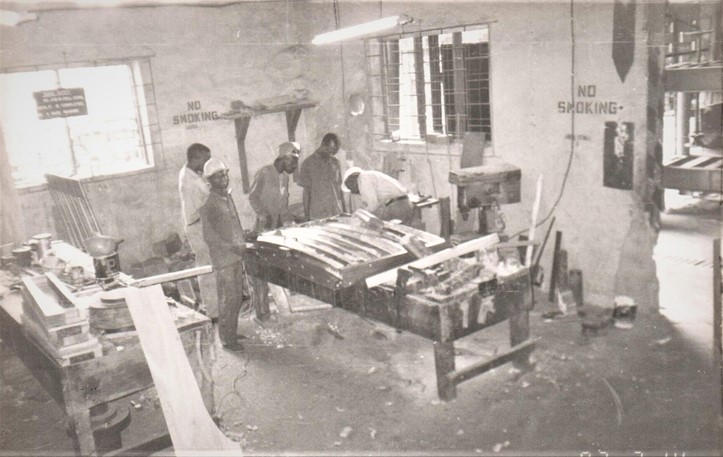
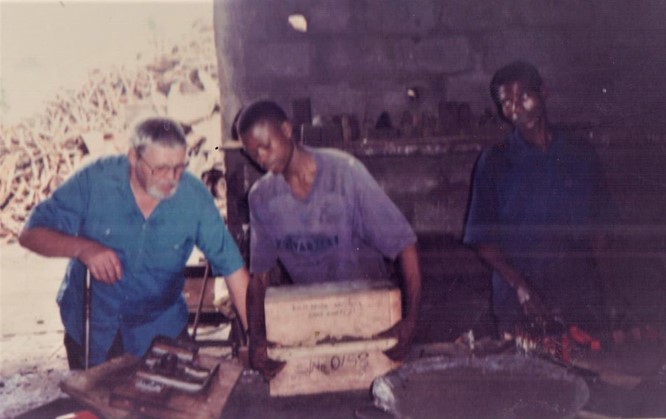
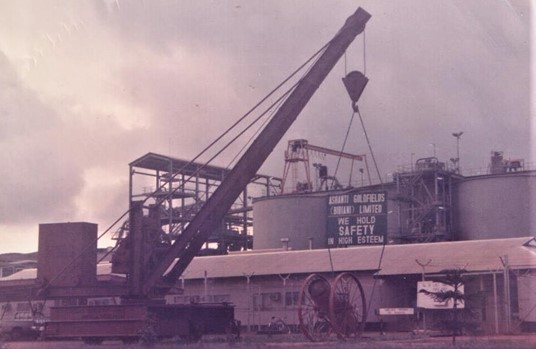
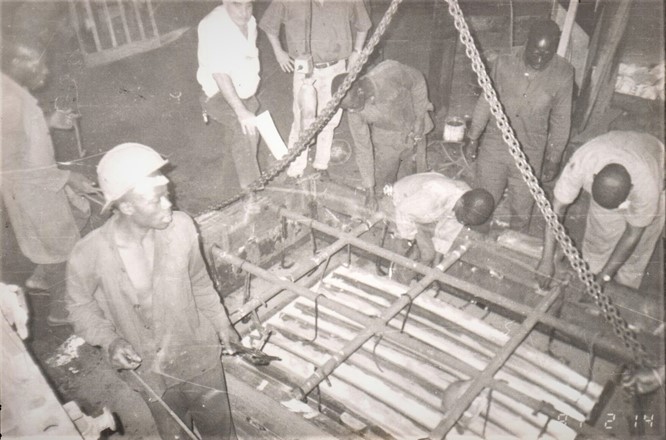
2000s
Innovation is the name, and export & expansion is the game.
In 2000, NFL got its ISO9001:1994 accreditation, the 50th Company in Nigeria, and the 1st foundry in sub-Saharan Africa. In 2002, NFL supplied all drainage gratings for Trains 4,5,6. This is NFL's first entry into the Oil & Gas industry, supported by SHELL and NLNG. In 2003, brother Romeo got monored by President Olusegun Obasanjo with the award of Member of the Order of the Federal Republic (MFR) in recognition of his outstanding contributions to the manufacturing sector, human resources development, and his efforts in the conservation and preservation of Nigeria's cultural heritage.
The newly formed Bank of Industry (BOI) funds the Otta expansion, which becomes operational in January 2005. In December 2006, NFL, along with 12 other organizations, register a not-for-profit company called Nexportrade Houses Ltd. The objective was to promote inter Africa trade and investment by creating trade houses in each African. Other shareholders include MAN, NACCIMA, NASSI, NASME, FNE, ECOBANK Plc, UBA Plc, NEPC, Flour Mills Plc, PZ Cussons Plc, Koinonia Ventures Ltd.
In 2007, Brother Romeo became a Member of the Presidential Committee on Concessions/Waivers & incentives, which results in the Export Expansion grant of today. By 2007 NFL founders create Metec West Africa Ltd (MWA) with a foreign partner, a non-ferrous foundry, to produce sacrificial anodes for the Marine & Oil & Gas Industry. By this time, the founder members showed their commitment to Nigerian Content before the signing of the NCOG Act of 2010. ExxonMobil was the first Independent Oil Company to accredit MWA after auditing. MWA, in 2007 is the only actual and accredited sacrificial anode manufacturer in entire Africa.
.
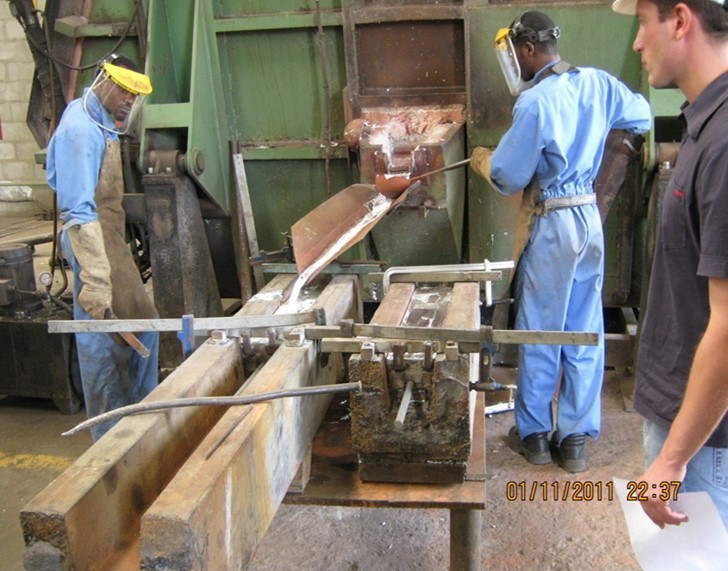
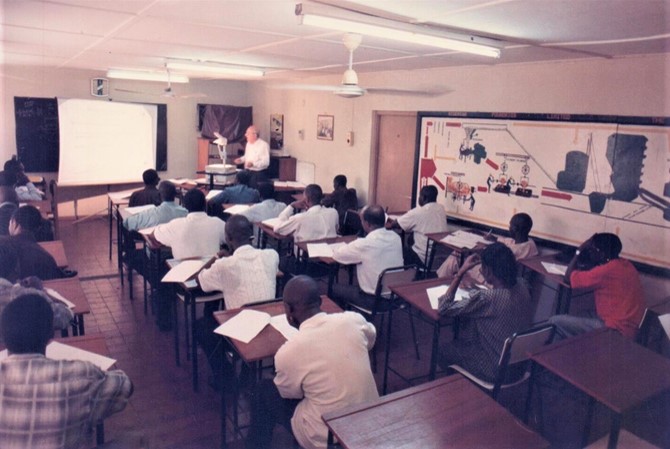
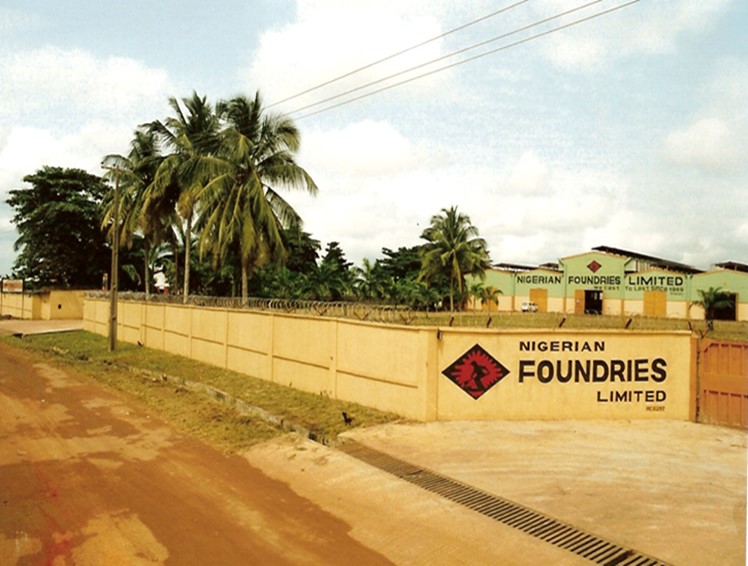
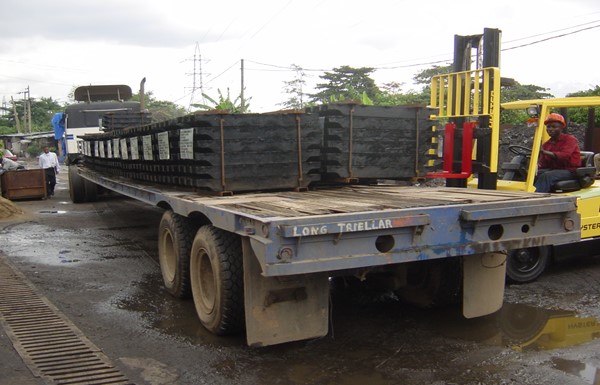
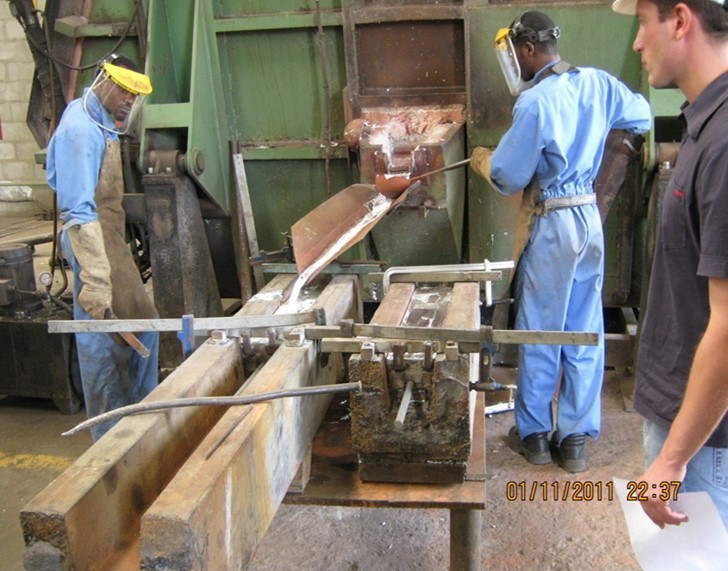
2010-2015
Transitions come in place for a stronger tomorrow.
In 2010 NFL gets certified for ISO9001:2008 and develops the technology to produce ductile iron. It becomes the 1st foundry in Sub-Sahara Africa to produce ductile iron products. By 2010 upon the signing of the NOG Act on Local Content, NFL takes the lead in Nigerian Content by setting up a non-ferrous foundry to produce sacrificial anodes. In April 2012, the 1st Founder Member, Mr. Romeo Barberopoulos, passes on.
In 2014 the merger of the Ilupeju plant to Otta became a reality through BOI funding. In 2015, through TOTAL and Saipem, the Egina Oil & Gas project became a game-changer for NFL. NFL successfully supplies 1200 tons of foundation ballast castings. At the same time, MWA produces and delivers the sacrificial anode requirements for the Egina Oil field. Part of the scope includes exports of Made-in-Nigeria anodes to Korea for the Egina FPSO.
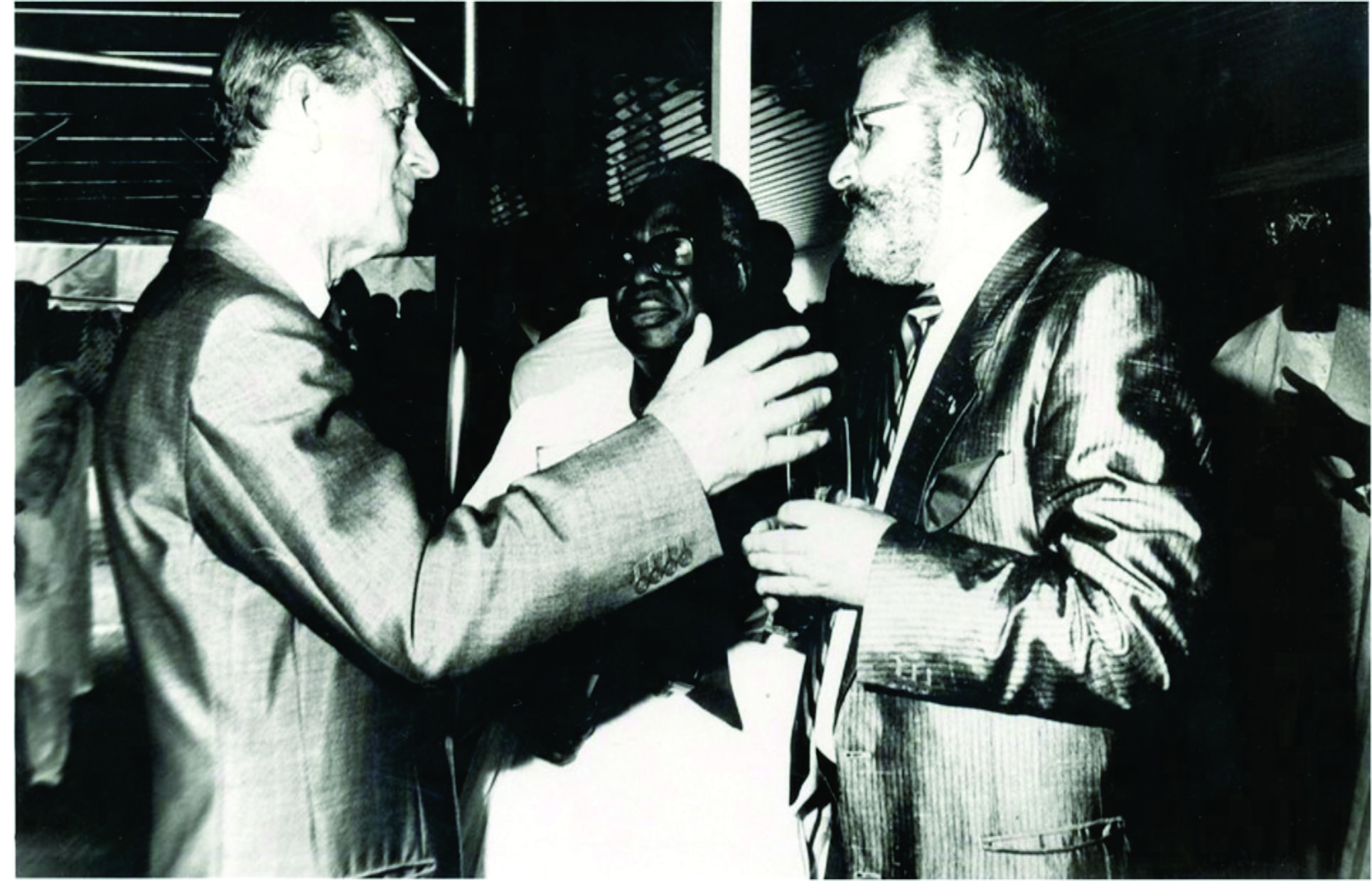
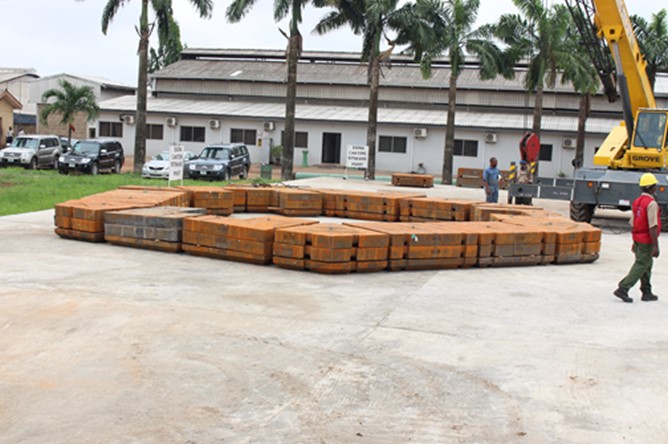
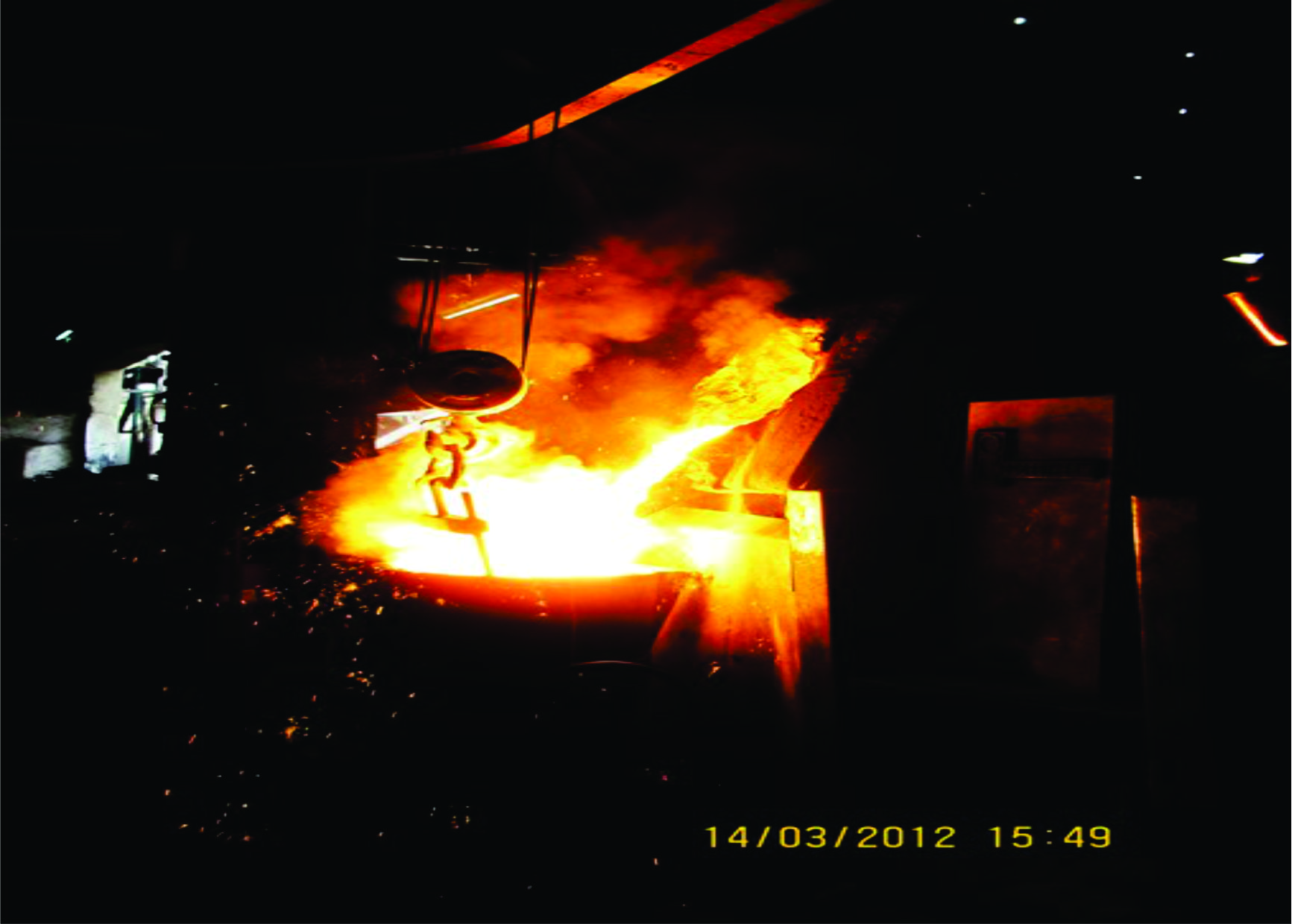
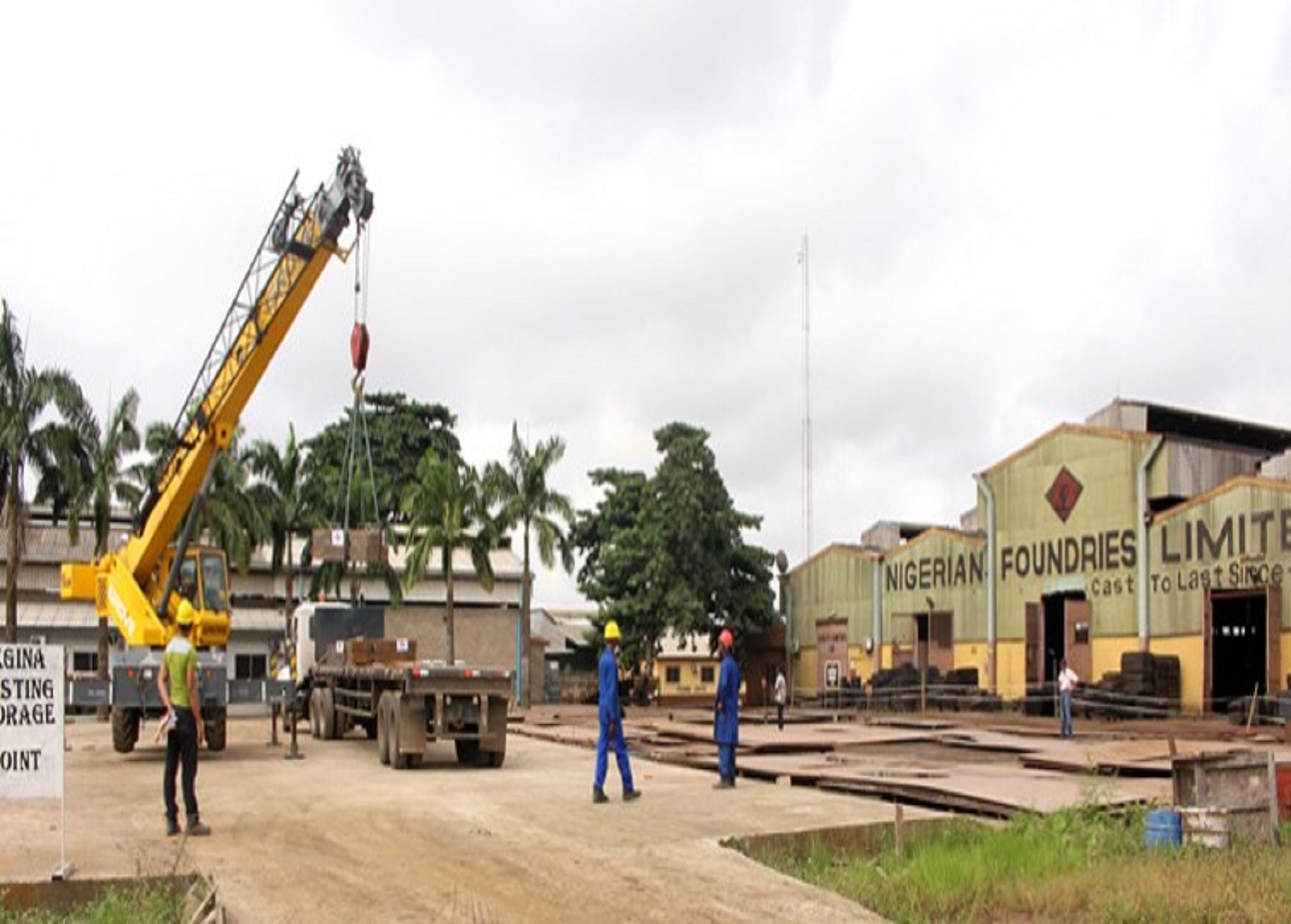
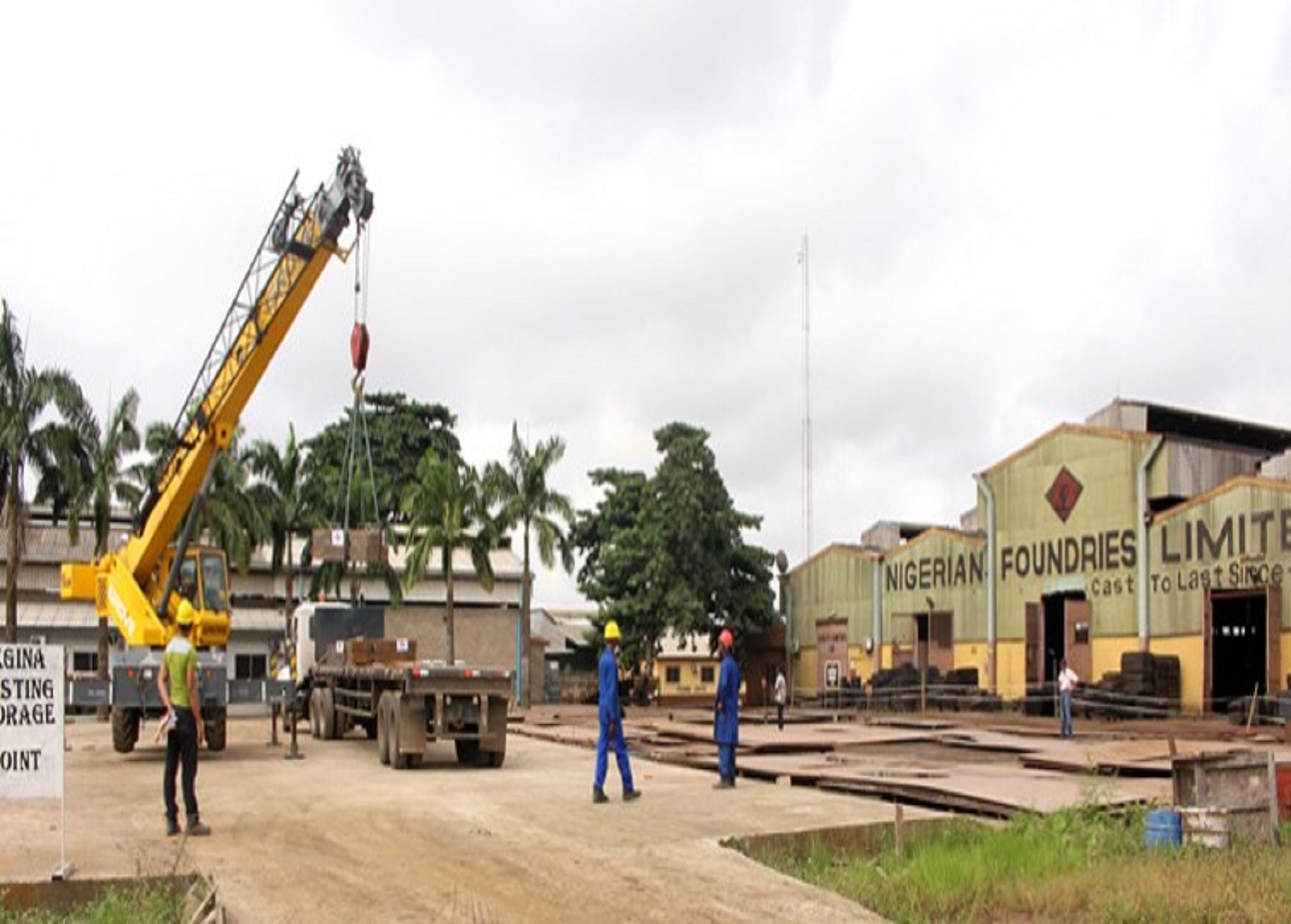
2016-2019
Seamless transition to 2nd generation. Beginning of new vision and strategy
On 22nd October 2016, the 2nd Founder member Mr. John Barberopoulos passes on. The Company entirely moves into the new generation. Oye and Nicholas take over the business. Both are USA University educated with respectively 35 and 17 years working experience in the Company.
The Company's Vision statement changes "To lead Africa's industries into the 4th industrial revolution through innovative technology by developing self-sustainability in manufacturing that transcends centuries ahead!"
Investments are made into Additive Manufacturing (3d printing) and Laser scanning to improve the production of intricate castings. NFL produces the first-ever valve bodies in West Africa under the inspection of the Nigerian Content Development & Monitoring Board (NCDMB). NLNG supports NFL and awards a contract to produce 8 x 10-ton industrial calibrated weights for their large cranes. The American Foundry Society (AFS) recognizes NFL's innovative initiatives and invites the MD to make a presentation on "the experiences of an African Foundry in additive manufacturing." at the 2nd Additive Manufacturing for Metal Casting Conference held in Kentucky, USA.
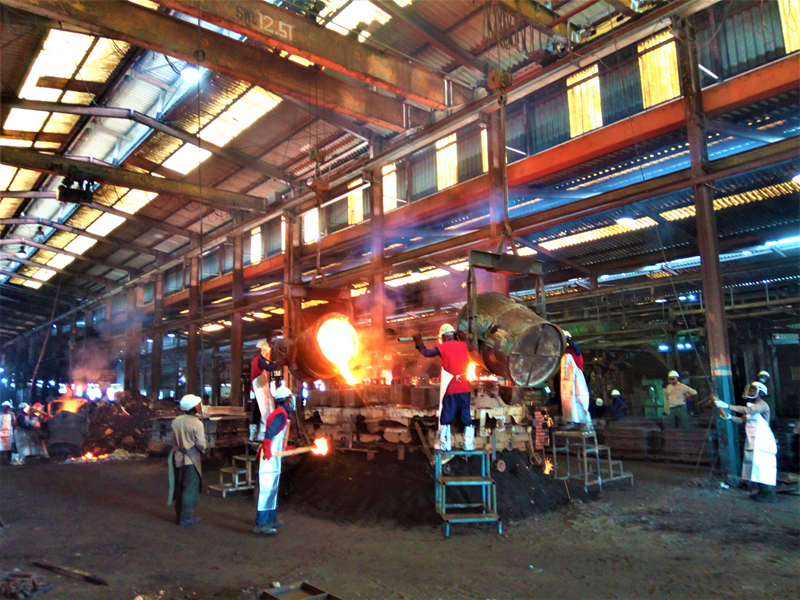
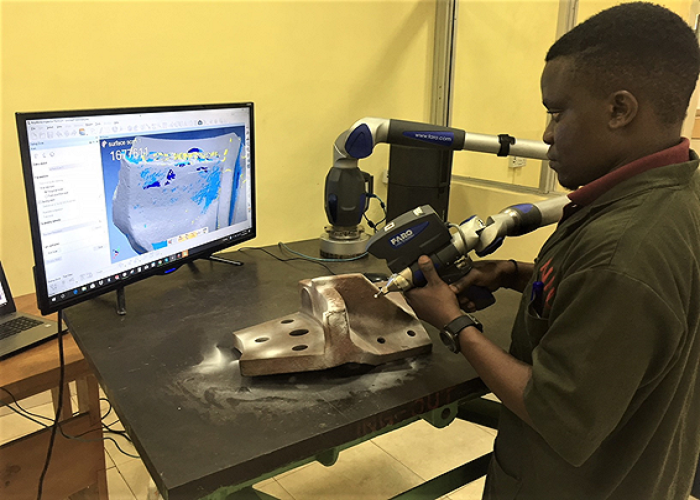
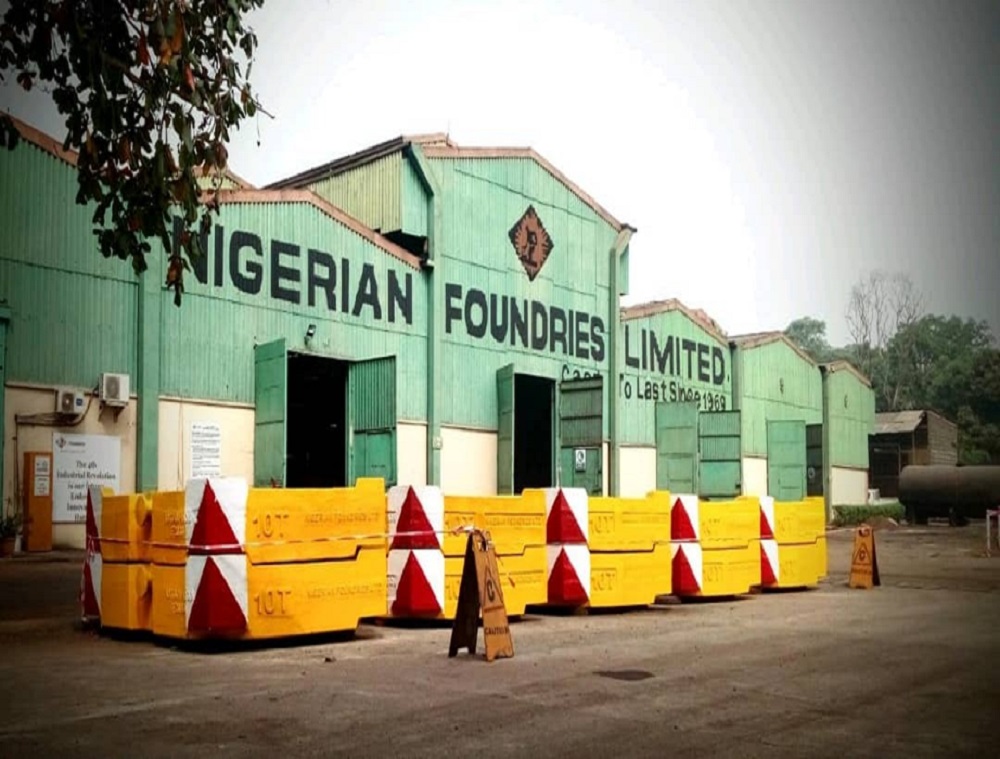
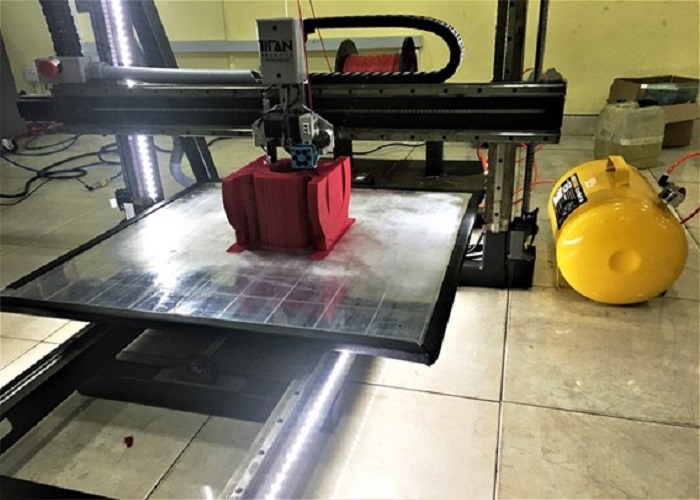
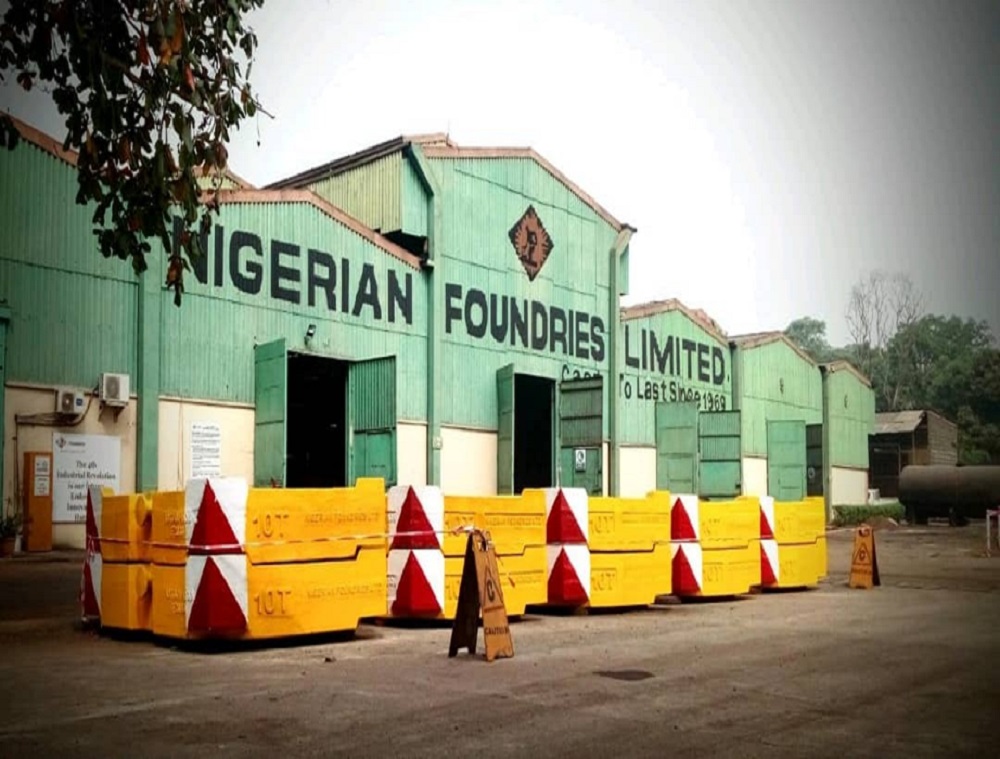
2020-2021
The Covid19 Pandemic years: Resilience, Adaptability, Optionality: The way forward; Cre-action!
By By January 2020, with the Covid19 pandemic, the company braces for Resilience, Adaptability, and Optionality. NFL gears up to support regional industries with locally made parts and components. The machine and fabrication shop get upgraded.
NFL and its two sister company activities get rebranded as the Nigerian Foundries Group (NFG). By 2021, the Nigerian Foundries Education Foundation is formed to educate Nigeria's youths in Innovation, Design, and Additive/Digital manufacturing technologies. NFL creates the Orisha Mazda educational module for high schools, Universities, and Organisations that want to educate students in 3D printing and foundry manufacturing. It includes a 3D printer and a non-ferrous micro foundry. The Orisha Mazda module is a unique educational concept created for Africa to promote innovation. NFL becomes instrumental in the founding of the Additive Manufacturers Association of Africa (AMAA).
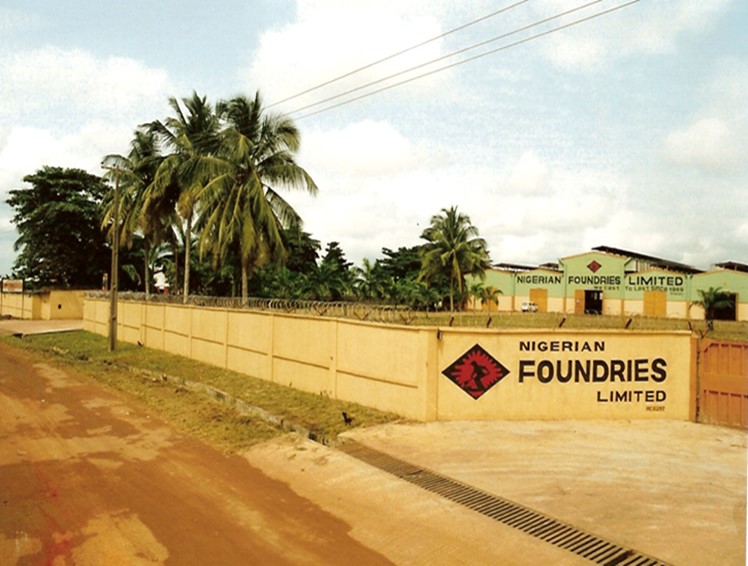

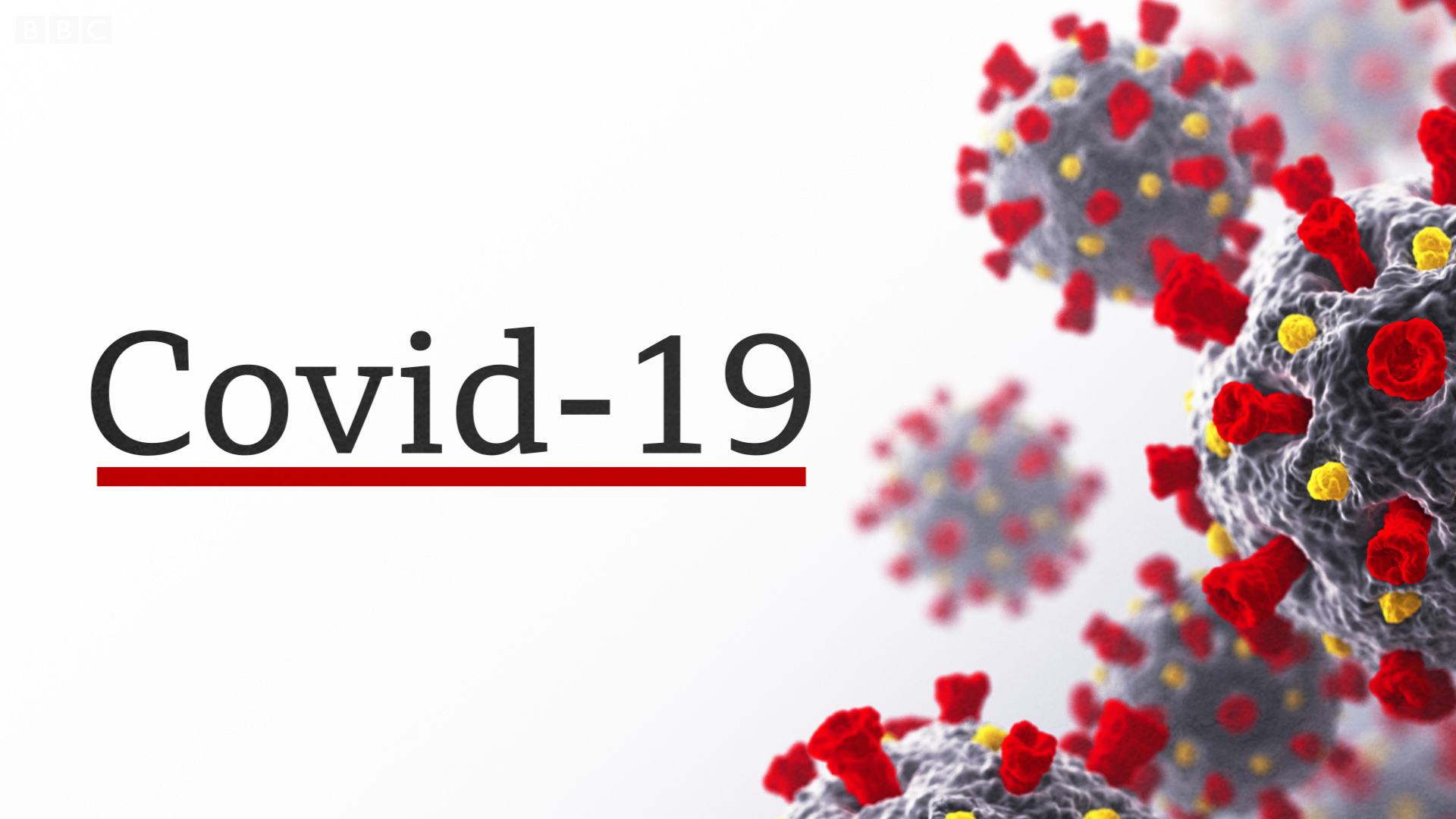
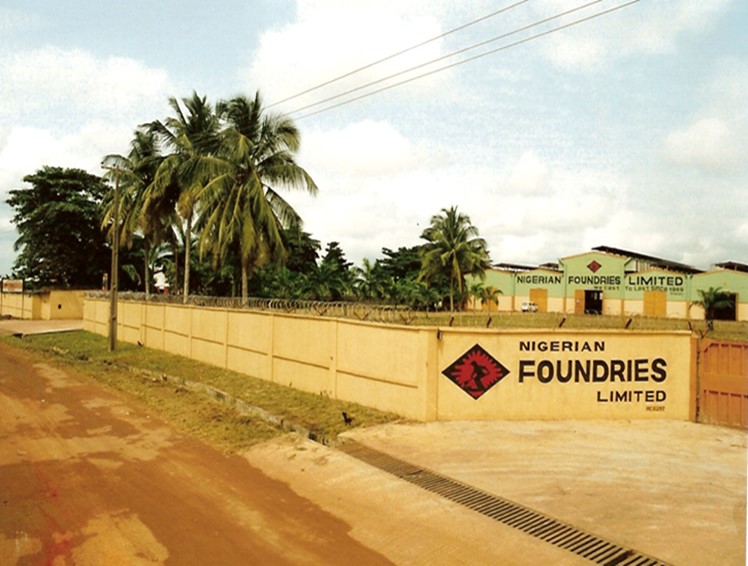
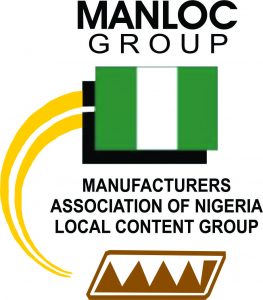
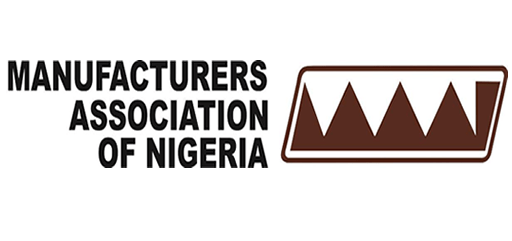
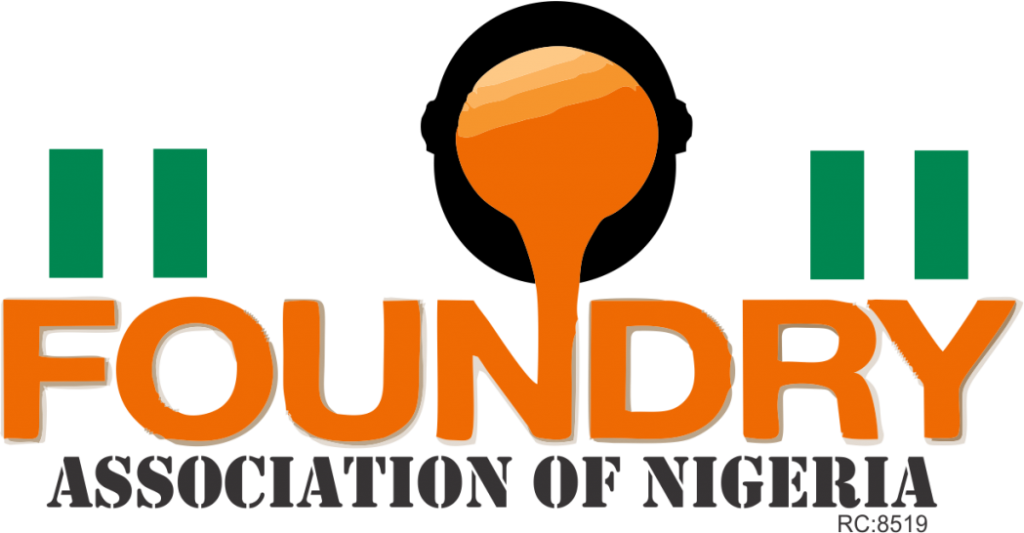
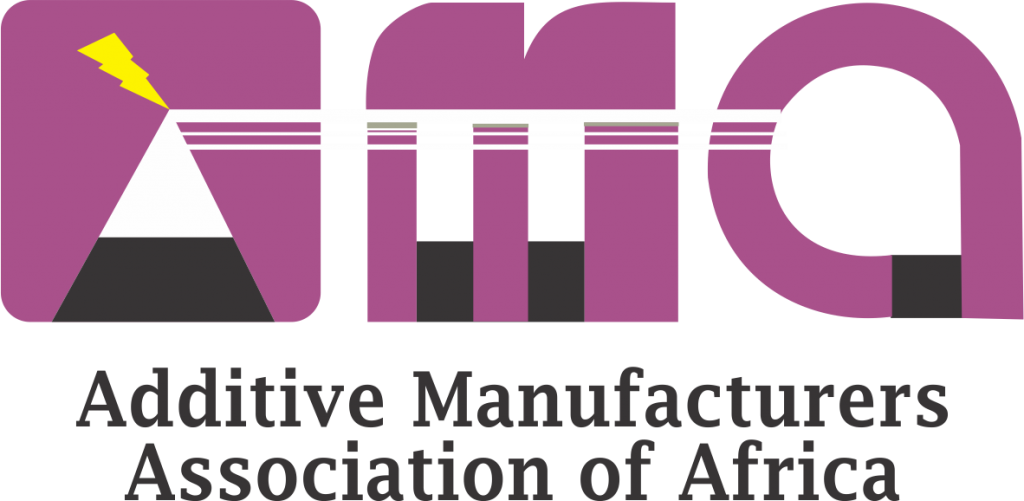